概要
鋼構造物の新設や、塗替工事における素地調整は、予算,環境問題(粉塵・騒音)、鋼構造物の形状等の諸事情で、ブラスト処理などの高度な素地調整を実施することが困難でした。
しかし、エポガードシステムは、2~3種ケレン程度の簡単な素地調整でも長期にわたって防食性の維持を可能にしました。あらゆる鋼構造物の内部から錆を無力化する最新の防錆・防食処理システムです。
特徴
- 塗装サイクルの長期化実現。
- ライフサイクルコスト(LCC)の低減。
- 腐食の原因となる赤錆(不安定錆)を防食性を有する黒錆(安定錆)に転換する技術です。
*例) 南部鉄瓶などがあります。
- エポガードシステムの採用での再塗装の場合は、素地との密着性に優れているためケレン作業が不要となり、従来工法に比べ作業時間が50%短縮可能となります。
- 人件費、経費の削減
- 有害な重金属(クロム、鉛)などは含まれておりません。
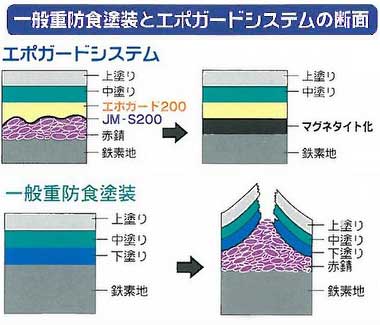
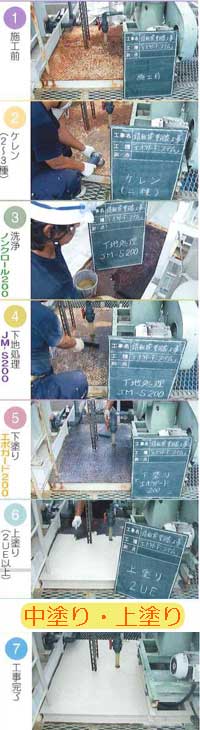
一般重防食塗装とエポガードシステムの工程比較
エポガードシステム
簡単な素地調整(2~3種ケレン程度)でも優れた防食性を発揮します。高浸透性の下地処理剤(JM-S200)と特殊変性エポキシ樹脂プライマー(エポガード200)との 相乗効果により、鉄素地まで強力に浸透し、錆を固定化させ、緻密で安定な黒錆(マグネタイト)に転換します。また再塗装のサイクルを延長し、 再塗装の際の素地調整を簡略化することができ、メンテナンス費用の大幅な削減が可能です。
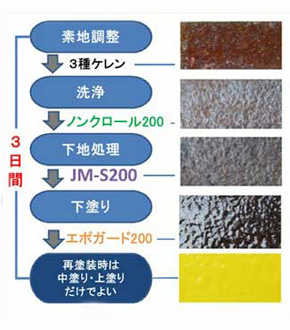
一般重防食塗装
一般的な重防食塗装では、塗装前に十分な下地処理(2種ケレン以上、サンドブラスト等<鋼道路橋再塗装>)を行うことが必須条件ですが、補修 や塗替えでは環境汚染など様々な制約から十分な下地処理ができないのが実情です。
錆の残存面に塗装しても長期の防食性が維持できず、短時間に塗膜下で腐食が進行し、塗膜が錆屑を抱いて剥がれてしまいます。そのため、再塗装 の度に下地処理から始まる全工程をやり直す必要があります。
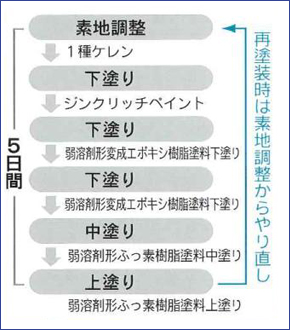
エポガード200・キレート剤の楔(くさび)効果
下図で表したように、エポガード200に含有されるキレート剤は、楔(くさび)効果、つまりアンカーボルトのような役割を持ち、 それぞれが離れないこととなります。
例えば、再塗装時に活膜と鉄素地が両方存在した上にエポガード200を塗布した場合、その全体を被膜することで、そのキレート効果により エポキシ樹脂の中で互いに結合しあい離れなくなります。
キレート剤は、鉄素地に食い込むこととなり、被膜されたエポガード200の外部より錆(Fe2O3)の原因となる水、空気、酸、アルカリを内部に侵入させないため、耐候性に優れていると言えます。
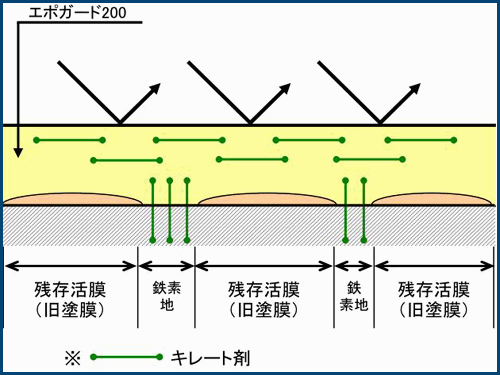
複合サイクル試験
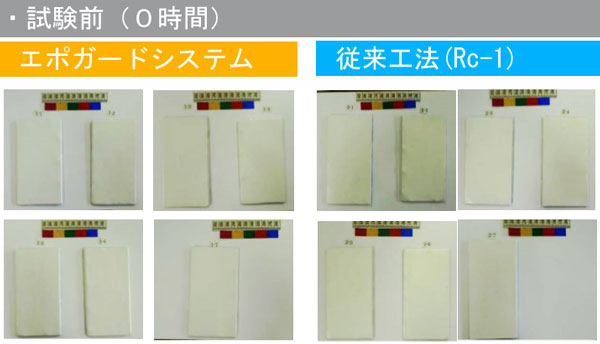
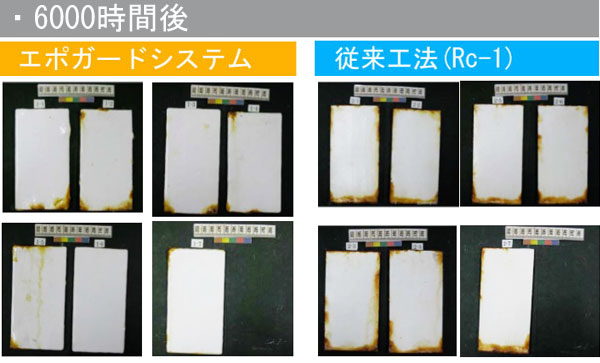
試験報告書
-
- ≪研究結果及び考察≫
試験を開始してから1,500時間ごろから従来工法の供試体で角や縁に微小な錆が見ら れるようになった。2,500時間経過時からエポガードシステムの方にも錆が少しずつ見ら れるようになった。2500時間時点でエポガードシステムと従来型工法を比較すると、従 来型工法の方がより腐食が進んでいるようである。4000時間経過時にも、従来型工法の 方がエポガードシステム工法よりも錆が進んでいるようである。5000時間経過時からは両 工法の発錆状況に、顕著な違いは認められない。ただし、エポガードシステム工法の1-6 供試体は6000時間経過時でもあまり錆が見られない。 膜厚は測定した値を1000時間 毎にグラフにしてある。グラフの多くが3000時間で低い値を示しているのは、3000時間時 だけ別の膜厚計を使用したためだと考えられる。その点を除くと、膜厚の値はほぼ変化せ ず同程度の値を示していると判断できる。 以上のように、単純に本実験の結果をみる と、従来工法(RC-I)に比べ、エポガードシステムの方がやや腐食耐久性に優れていると 考えられる。しかし,今回用いた供試体は、表裏が同じ仕様となっているわけではないの に加え、エポガードシステム供試体と従来工法供試体では裏面の処理が異なっているた め、本実験において錆はすべてエッジ部から発生していることを考えると、両面の 塗膜境界部の処理状況が発錆状況の違いを生じさせた可能性も否定できない。 今後,さらに実験を実施する場合、この点に留意して実験計画を立案する必要がある。
- メーカーサイト: 株式会社エコクリーン